در این مقاله روی شوت های انتقال مرسوم متمرکز می شویم: عملکرد، طراحی و ویژگی ها. در مورد روش های مختلف مدیریت ایمن جریان مواد، کاهش سایش و کنترل جریان هوا برای حداقل کردن غبار و ریزش مواد و حفظ عمر شوت های انتقال بحث می کنیم. یک رابطه برای محاسبه زوایای کنج شوت های انتقال یا هاپر نیز ارائه شده است.
یک کانوایر مواد را از کانوایر دیگر، مخزن ذخیره، فیدر، واگن یا دیگر سیستم های حمل مواد دریافت کند. اگرچه منبع تأمین مواد ممکن است متفاوت باشد اما تقریبا همیشه مواد از میان تجهیزی که شوت های انتقال گفته می شود، به کانوایر دریافت کننده منتقل می شود. این فصل طراحی شوت های انتقال های مرسوم را شامل می شود.
ویژگی ها و عملکرد شوت های انتقال مرسوم
شوت های انتقال مرسوم، در صورت انجام مقاصد زیر ماموریت خود را انجام داده اند:
- برقراری انتقال مواد بالک با نرخ طراحی بدون گرفتگی
- حفاظت پرسنل در برابر سوانح
- حداقل کردن نشتی مواد
- برگرداندن مواد خراشیده شده از نوار به جریان اصلی
- سرویس کاری آسان service-friendly
با توجه به اینکه کانوایرها معمولا به تنهایی نیستند و جزئی از یک سیستم پیچیده هستند، غالبا لازم است که مصالحه ای صورت پذیرد. در نتیجه این مباحث الزامات مطلق نیست، بلکه اهدافی برای طراحی شوت های انتقال مؤثر هستند.
روش های طراحی سرانگشتی زیادی برای طراحی شوت های انتقال مرسوم برحسب اصول مهندسی و تجربی وجود دارد. گاهی این روش ها با یکدیگر توافق یا تضاد دارند. طراحی شوت های انتقال، ترکیبی از علم و هنر است.
بنابراین عاقلانه است با یک مهندس کانوایر با تجربه بابت طراحی سیستم یک کاربرد خاص انتقال مواد، مشورت شود. در ادامه مقاله به شرح مفصل ویژگی های شوت های انتقال مناسب خواهیم پرداخت.
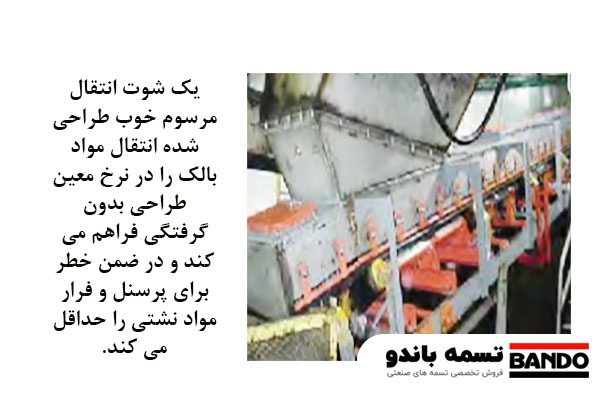
انتقال مواد
اولین وظیفه شوت های انتقال قابل اعتماد یک جریان مشخص مواد بالک است. اگر مواد با قابلیت اعتماد از شوت های انتقال جریان نیابد، به هیچ کدام از این مقاصد نخواهیم رسید.
جریان مواد بالک از شوت های انتقال، باید پیوسته و هموار انجام شود. شوت های انتقالی که حجم انبوهی از مواد را به یکباره روی نوار میریزد، مشکلات متعددی برای کانوایر بوجود خواهد آورد.
تخلیه متناوب مواد روی نوار شاید باعث انتقال مرکز جرم و در نتیجه انحراف نوار شود. همچنین افزایش ناگهانی بار می تواند باعث تنش بیش از حد به اجزای کانوایر، به ویژه موتور محرک یا سیستم نگهدارنده نوار نقاله شود و اگر سطح مقطع شوت های انتقال خیلی کوچک باشد، مشکلات گرفتگی را بوجود آورد.
امروزه روش های جدید، مثل روش مدلسازی المان گسسته با کامپیوتر، برای بررسی قابلیت اعتماد جریان مواد در دسترس است. طراحی اکثریت قریب به اتفاق شوت های انتقال های مرسوم هنوز بر اساس قوانین سرانگشتی انجام می شود.
حفاظت پرسنل
هرچند انتقال های روباز در برخی صنایع مثل شن و ماسه و معادن زیرزمینی معمول است، روند طراحی شوت های انتقال معمول بر اساس محصور کردن نقطه انتقال تا حد امکان از پولی تخلیه تا مسافتی از کانوایر دریافت کننده می باشد.
محصور کردن ساده نقطه انتقال، روش مؤثری برای دربرگرفتن جریان مواد، کاهش فرار مواد نشتی، کاهش نویز، و جلوگیری از در معرض قرار گرفتن پرسنل در برابر بسیاری نقاط گلوگاه کانوایر می باشد.
حداقل کردن فرار مواد نشتی
اندازه محفظه اغلب بر اساس فضای موجود می باشد که ممکن است کمتر از فضای موردنیاز طراحی باشد. شوت های انتقال باید به مقدار کافی بزرگ باشد که اجازه هرگونه سرویس موردنیاز را بدهد.
همچنین باید به اندازه کافی بزرگ باشد تا این حجم کافی بتواند فشار مثبت و سرعت جریان هوا از داخل شوت های انتقال و در نتیجه انتشار غبار را کاهش دهد.
تعدادی عناصر طراحی مرتبط وجود دارد که روی تولید مواد نشتی به شکل غبار و ریزش مواد تأثیر می گذارد. یک فاکتور کلیدی در کاهش فرار مواد قراردادن بار در مرکز نوار است.
بارگیری خارج از مرکز (ریختن بار بطور عمده در یک سمت نوار) مشکل بسیاری از نقاط انتقال است که باعث نشت مواد می شود.
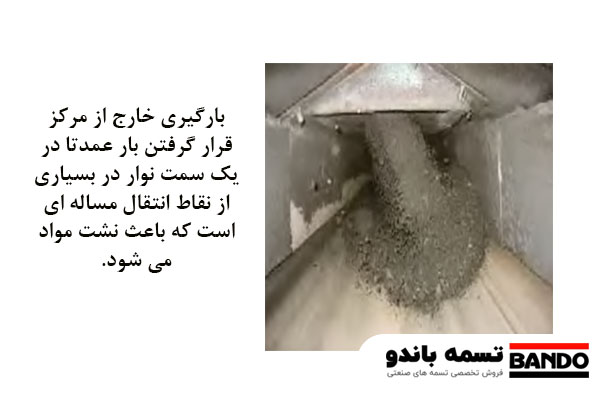
این مسئله در نقاط انتقال غیرخطی، با تغییر جهت حرکت مواد، مشهورتر است. همچنین بارگیری خارج از مرکز در نقاط انتقال همراستا نیز می تواند وجود داشته باشد.
جاییکه مواد در شوت های انتقال جمع می شود یا وقتیکه تغییرات در مشخصات مواد (مثل رطوبت، اندازه ذرات، یا سرعت) مسیر مواد را تغییر می دهد و باعث جمع شدن بیشتر مواد در یک سمت نوار می شود. این جابجایی باعث مشکلات مسیریابی نوار و در نتیجه ریزش بار از لبه نوار به بیرون نقطه انتقال می شود.
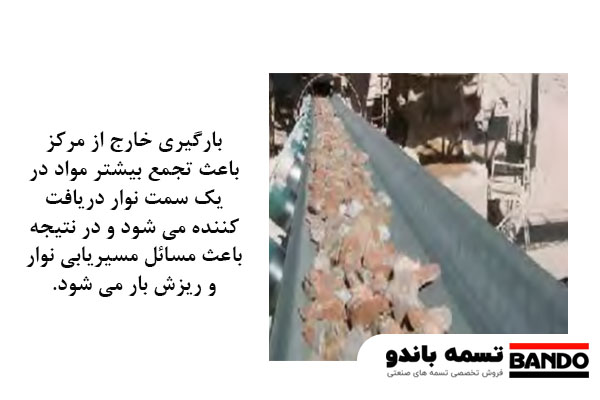
اگرچه ایده آل، طراحی شوت های انتقال بدون مشکل ریزش خارج از مرکز بار است، اما راه حل هایی برای جبران آن در ناحیه بارگیری وجود دارد. توانایی رولیک های هدایت کننده و دیگر سیستم های تنظیم کننده نوار در مقابله با ریزش خارج از مرکز بار محدود است. برای کسب اطلاعات بیشتر در مورد خرید رولیک ها می توانید به سایت تسمه نقاله باندو مراجعه نمایید.
نصب تجهیزات اصلاحی مثل منحرف کننده deflector یا کمک کننده های جریان در داخل ناحیه بارگیری به همراه سیستم های تنظیم کننده نوار یک رویکرد مؤثر را فراهم می کند.
تعدادی تجهیزات جانبی (مثل منحرف کننده، لاینر، سپرک، تیغه، سرند، میله های گریزلی یا بستر بار مرده) در داخل شوت های انتقال می تواند به جهت دادن جریان مواد کمک کند و یک الگوی بارگیری بالانس شده فراهم کند.
آن ها بعدا در این مقاله بررسی می شود. هندسه بدنه شوت های انتقال باید هنگام طراحی شوت های انتقال بر اساس الگوی جریان مواد موردانتظار محاسبه شود تا بارگیری در مرکز را بهبود دهد.
برگشت مواد تمیزشده از روی نوار به جریان مواد
تمیزکن های نوار در پولی تخلیه نصب می شوند تا موادی که بعد از نقطه تخلیه به نوار چسبیده است را پاک کند. موادی که با تمیزکن ها برداشته می شوند باید به جریان مواد برگردانده شود تا روی دیواره شوت های انتقال یا دیگر اجزای کانوایر جمع نشود. در مقاله خرابی کانوایر و مشکلات نوار نقاله ها می توانید با خرابی نوارنقاله دراثر استفاده نادرست از تمیزکن ها بیشتر آشنا شوید.
در نتیجه معمولا شوت های انتقال دریبل بزرگ با دیواره شیبدار که سیستم تمیزکن نوار را ببندد، لازم است تا مواد پاک شده را همراهی نموده و به جریان اصلی مواد هدایت نماید. این مواد چسبندگی زیادی دارند، بنابراین ممکن است شیب دیواره های شوت های انتقال دریبل، خیلی زیاد و تقریبا قائم باشد.
اجرای این طرح ممکن است نیاز به شوت های انتقال خیلی بزرگ، لاینرهای اصطکاک پایین، و یا تجهیزات جانبی مثل شوت های انتقال دریبل ویبره، دمنده های هوا و کانوایرهای برگشتی داشته باشد.
هنگام طراحی یک نقطه انتقال باید توجه داشته باشید که کمترین شیب، زاویه کنج valley angle بین دو دیواره شوت های انتقال است.
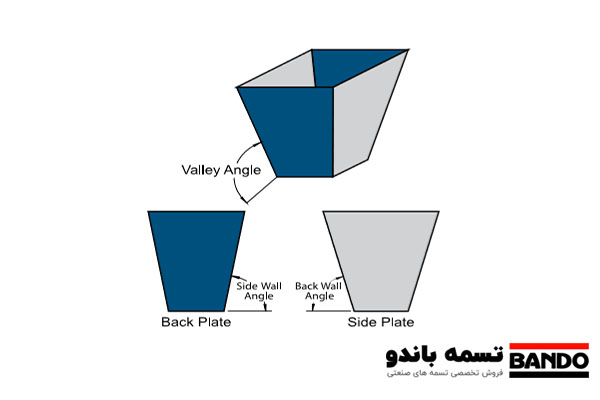
برای حداقل کردن چسبیدن مواد برگشتی، زاویه های کنج باید تندتر شود، یعنی زاویه دیواره ها تندتر شوند. برای بدست آوردن یک زاویه کنج معین، زاویه دیواره ها حتی با شیب تندتر نیاز است. هرجا امکان پذیر باشد،گوشه ها باید گرد شود تا احتمال گرفتگی ذرات ریز را کاهش دهد.
سرویس کاری آسان شوت های انتقال
طراحی شوت های انتقال بگونه ای که اجزا برای سرویس به آسانی در دسترس باشند، جهت تعمیرات نگهداری کارآمد حیاتی است. اغلب این کار ساده است.
با طراحی سازه منطبق با محل ترجیحی اجزا یا فراهم کردن یک وسیله برای بلند کردن قطعات سنگین دیواره شوت های انتقال یا دیگر اجزایی که نیاز به سرویس داشته باشد.
بسیاری از تأمین کنندگان چیدمان اجزای تجهیزات خود را با سرویس کاری آسان (سرویس پسند) ایجاد می کنند اما با نصب لوله کشی تأسیسات و دیگر اجزای کارخانه از بین می رود.
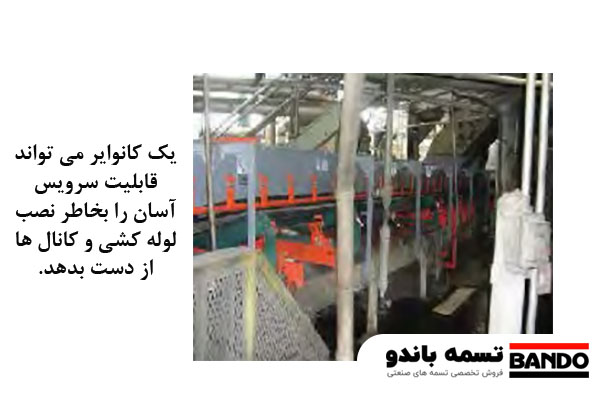
فراهم کردن دسترسی کافی و پلت فرم در ارتفاع مناسب، به سادگی سرویس کاری آسان را برای شوت های انتقال ایجاد می کند.
اغلب لازم است داخل شوت های انتقال برای تعمیرات، داربست و پلت فرم زده شود. ممکن است زدن داربست و برچیدن آن از خود تعمیرات بیشتر زمان بگیرد. نصب تکیه گاه برای گذاشتن پلت فرم داخل شوت های انتقال (به دور از جریان مواد) روش مفیدی برای کاهش زمان می باشد.
طراحی شوت های انتقال بگونه ای که بتوان تعمیرات اجزای بحرانی را بدون ورود به فضای محدود confined- space یا مجوزهای کار گرم (بریدن و جوشکاری) hot work permitانجام داد، بهره وری تعمیرات را افزایش خواهد داد.
شوت های انتقال که تعمیرات نگهداری و تمیزکردن آن ها آسان باشد، تمیزتر می باشد و بنابراین تولید بیشتر و توقف کمتری خواهد داشت. به طور کلی برای کسب اطلاعات بیشتر می توانید به صفحه تعمیرات و نگهداری نوار نقاله ها مراجعه نمایید. و در صورت تمایل به خرید انواع چسب و قطعات یدکی نوارنقاله جهت تعمیرات، می توانید با بازرگانی باندو تماس بگیرید.
فاکتور های طراحی شوت های انتقال
چون هر ماده و هر کاربردی ویژگی های خاص خود را دارد، شوت های انتقال کارآمد باید بیشتر از یک ظرف توخالی باشند که مواد از آن عبور می کند. شوت های انتقال خوب طراحی شده مسیر مواد را کنترل خواهند کرد، مانع گرفتگی می شوند و هزینه های تعمیرات نگهداری را حداقل می کند.
طراح شوت های انتقال مؤثر نه تنها باید به خصوصیات مواد، که ممکن است طی زمان تغییر کند، توجه داشته باشد بلکه باید اثر متقابل دیگر اجزای مختلف سیستم را لحاظ کند. بنابراین در ادامه این مقاله قصد داریم به ارائه نکات مربوط به طراحی شوت های انتقال بپردازیم.
طراحی شوت های انتقال مرسوم
طراحی شوت های انتقال مرسوم conventional transfer- chute design بطور معمول توسط طراح باتجربه یا مهندس انتقال مواد با استفاده از قوانین سرانگشتی پذیرفته شده، انجام می شود. بسیاری از شرکت های مهندسی قوانین طراحی خودشان را ایجاد کرده اند.
بسیاری از صنایع روش های ثابتی منطبق با نیازهای خودشان ایجاد کرده اند. هرچند این قوانین مختلف ممکن است فرق داشته باشند، اما توافق عمومی بر سر بسیاری از الزامات طراحی شوت های انتقال های مرسوم وجود دارد. دستورالعمل هایی برای طراحی شوت های انتقال های مرسوم در چند مرجع چاپ شده است. خلاصه ای از قوانین معروف طراحی شوت های انتقال در اینجا آمده است.
شوت های انتقال مرسوم معمولا از قسمت های اصلی زیر تشکیل شده است:
- شوت های انتقال سر: ناحیه ای که پولیِ سرِ نوار تغذیه کننده را احاطه می کند.
- شوت های انتقال ریزش: ناحیه ای که مواد در حال سقوط می باشند.
- شوت های انتقال بارگیری: ناحیه ای که مواد با نوار دریافت کننده برخورد می کند (ناحیه بارگیری load zone نیز گفته می شود.)
- ناحیه نشست: اگرچه از نظر فنی جزو شوت های انتقال نمی باشد، ادامه بدنه شوت های انتقال متصل به شوت های انتقال برای نشست غبار معلق در هوا می باشد.
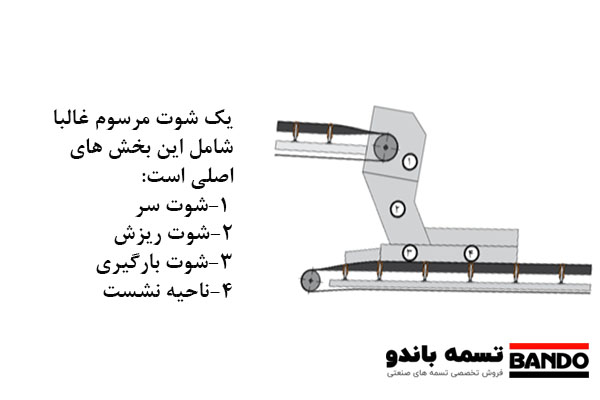
پارامترهای سیستم
داده های زیر حداقل هایی است که طراح باید قبل از شروع طراحی شوت های انتقال بین دو کانوایر داشته باشد:
- نرخ ظرفیت (تن بر ساعت t/h)
- محدوده شرایط محیط کاری
- دانسیته بالک هنگام عبور – کیلوگرم بر مترمکعب (kg/m3)
- دانسیته بالک آزاد – کیلوگرم بر مترمکعب (kg/m3)
- طبقه بندی مواد بالک-توزیع ابعادی ذرات، مشخصات مواد و هرگونه شرایط خاص
- عرض، سرعت، و زاویه تغاری نوارهای تخلیه و دریافت کننده
- سطح مقطع بار روی نوار – مترمربع m2(ft2)
- فلوشیت فرایند نشان دهنده ترتیب کانوایرها
- نقشه چیدمان عمومی شامل نما بالا و روبرو، ابعاد مهم، و ارتباط کانوایرهای تخلیه و دریافتی
در بسیاری از موارد، ظرفیت ذکر شده برای کانوایر به دلایل مختلف 10 الی 20 درصد کمتر از ظرفیت واقعی مهندسی شده است. درنظر گرفتن ظرفیت بیشتر برای ضریب اطمینان است و موجب گذراندن بارهای زیاد ناگهانی و کاهش ریزش مواد می شود. هنگام تعیین اندازه شوت های انتقال، باید نوار پر از بار درنظر گرفته شود.
زاویه قرار مواد اغلب به عنوان زاویه اصطکاک داخلی و رابط در طراحی شوت های انتقال بکار می رود. زاویه قرار برای تعیین حداقل شیب دیواره شوت های انتقال و ارتفاع تپه مواد در داخل اسکرت بکار می رود. بعلاوه زاویه قرار برای محاسبه بار بالای سر head load یا وزن مواد روی نوار که باید با یک هاپر پر از بار شروع به کار کند، بکار می رود.
اگرچه زاویه قرار بطور گسترده ای برای این محاسبات بکار می رود، استفاده از زاویه قرار برای این محاسبات غیرقابل قبول است، چون زاویه قرار بیانگر قابلیت چسبیدن مواد به یکدیگر یا دیواره نمی باشد.
یک مسیر بهتر آزمایش خواص واقعی مواد هنگام عبور از میان سیستم می باشد. این آزمایش مواد، محدوده خواص مواد بالک که شوت های انتقال باید با آن همراهی کند را تعیین می کند. همچنین به حذف مشهورترین اشتباهات طراحی شوت های انتقال کمک می کند.
خط سیر مواد
خط سیر (مسیر) مواد بالک از وقتی کانوایر تخلیه را ترک می کند trajectory گفته می شود. خط سیر مواد تحت تأثیر سرعت نوار، زاویه شیب نوار تخلیه، و پروفیل مواد روی نوار می باشد.
در طراحی شوت های انتقال مرسوم، خط سیر مواد رسم می شود و به عنوان نقطه شروع برای تخمین اولین نقطه ای که مواد به بدنه شوت های انتقال برخورد می کند، استفاده می شود. از آنجا به بعد فرض می شود جریان مواد از دیواره شوت های انتقال مشابه یک پرتو نور که با آینه برخورد می کند، منعکس می شود.
مشهورترین اشتباه در این مرحله طراحی، رسم نادرست مسیر اولیه مواد و درنظر نگرفتن اثر اصطکاک هنگام کشیدن انعکاسات جریان مواد در برخورد با دیواره های شوت های انتقال است.
تفکر کنونی در طراحی شوت های انتقال کنترل جریان مواد است، بدون اینکه مواد سقوط آزاد نموده و با نوار دریافت کننده برخورد کند. با این رویکرد کنترل، طراح فرض می کند سطح مقطع مواد بطور قابل توجهی بازfan out or open up نمی شود. ارتفاع ریزش کاهش می یابد تا از دست رفتن کیفیت مواد، تولید غبار، و سایش روی نوار دریافت کننده کاهش یابد.
این رویکرد نیاز به دانستن اصطکاک بین مواد و دیواره شوت های انتقال دارد. برای کمک به طراح شوت های انتقال در ارزیابی اثر تغییر خواص مثل ضریب اصطکاک، coefficient of friction روش مدلسازی المان گسسته DEM در حال استفاده روی شوت های انتقال های مرسوم است. برای این هدف DEM متعددی در بازار وجود دارد.
فاصله، زاویه، و هم پوشانی بین کانوایرها
بطور ایده آل همه انتقال های نوار به نوار باید در یک خط باشد. نوارهای تخلیه و دریافت در یک جهت باشند. این نوع انتقال اجازه همپوشانی کافی بین نوارها برای جلوگیری از ریزش بار روی ناحیه گذار را می دهد، ناحیه ای که نوار از حالت تخت پولی انتها به شکل تغاری کامل درمی آید. همچنین انتقال به این شکل، مواد را در جهت حرکت نوار دریافت کننده تحویل می دهد.
بنابراین سایش و ریزش مواد را کاهش می دهد. اغلب انتقال های همراستا برای کاهش طول کانوایر وقتی قدرت موتور یا کشش موجود برای یک نوار ناکافی است یا برای همراهی کردن با فرایندهایی مثل مخلوط کردن blend، سنگ شکن crush یا جدا کننده seperate مواد است.
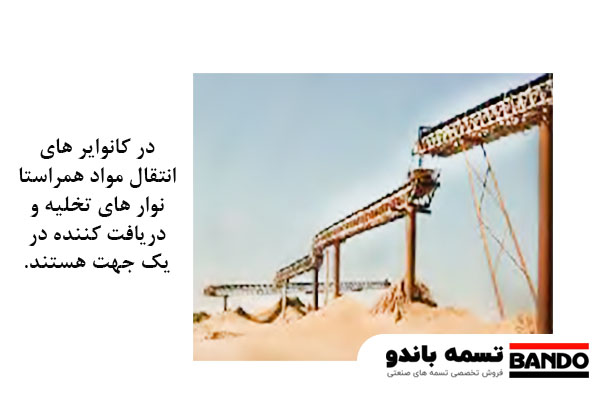
در اغلب اوقات هنگام بارگیری از یک کانوایر به کانوایر دیگر، یک تغییر در جهت مسیر حرکت نوار لازم است. ممکن است یک انتقال غیرخطی non-linear برای همراهی با تغییر جهت جریان مواد مثلا برای انبارکردن یا تقسیم مواد برای جداسازی لازم باشد.
مشکلات نقاط انتقال غیرخطی عبارت است از: سخت بودن حفظ سرعت، مسیر و زاویه مناسب مواد، مسائل کنترل غبار و ریزش و مسائل افزایش سایش و متعاقبا افزایش هزینه جایگزینی اجزای نقطه انتقال.
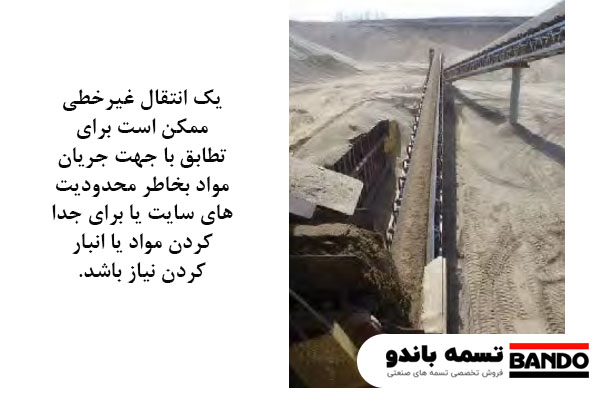
اگر مواد در جهتی که همراستا in line با حرکت نوار دریافت کننده نباشد، بارگیری شود، ممکن است اثر سایش روی دیواره شوت های انتقال سر (تخلیه) دیده شود. این اثر منطبق بر مسیر مواد است که سعی دارد بخاطر نوار دریافت کننده تغییر جهت و سرعت بدهد. اگرچه ممکن است اغتشاشات هنگام خروج مواد از اسکرت قابل رویت نباشد. اما به چپ و راست خوردن مواد داخل شوت های انتقال باعث افزایش سایش روی لاینرها، اسکرت، و سیستم درزبندی می شود.
نیروی بارگیری مواد ممکن است باعث انحراف نوار شود و آنرا به بیرون اسکرت براند، نوار درزبندی بیافتد و از برگشت نوار به مرکز جلوگیری کند. با تغییر بار، نوار سعی می کند به مرکز برگردد، به نوار درزبندی فشار وارد می کند و حجم زیادی از مواد به زمین می ریزد.
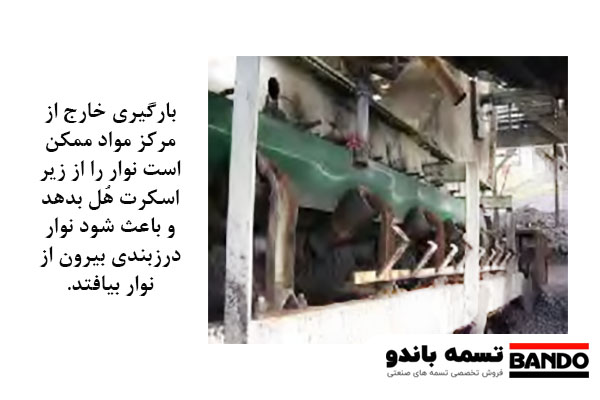
خوشبختانه روش های مختلفی برای هدایت مواد به جهت موردنظر و بارگیری نوار در مرکز وجود دارد. مشهورترین اشتباه در طراحی شوت های انتقال فراهم نکردن هم پوشانی کافی می باشد. این کار باعث ریزش بار در ناحیه گذار می شود و فضای کافی برای نصب تمیزکن های نوار نمی دهد. بدون توجه به طراحی مناسب کانوایر، شامل هم پوشانی کافی، کانوایری که اغلب گرفتگی، نشتی مواد و مشکلات زیاد سایش دارد، بر دوش فرایند می ماند.
ممکن است بارگیری در ناحیه گذار با هدف چند متر صرفه جویی در طول نوار انجام شود. این کار مشکلات زیادی در بارگیری، درزبندی، و سایش نوار ایجاد می کند و باید اجتناب شود.
باید توجه شود برای کاهش ریزش بار و غبار، باید ارتفاع سقوط مواد حداقل شود. هرچند طرح های کلاهک و چمچمه hood and spoon design از جاذبه برای حفظ سرعت جریان مواد استفاده می کنند و اغلب ارتفاع بیشتری نیاز دارند.
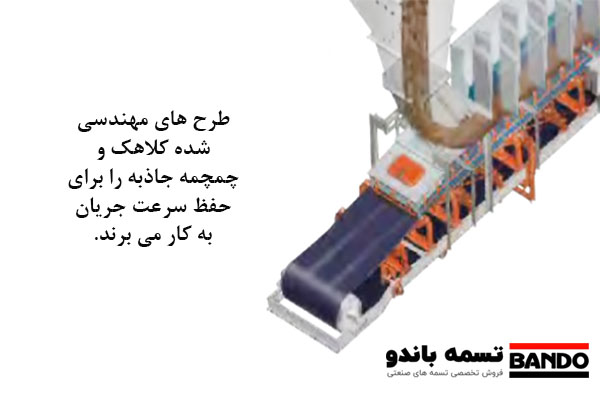